By Sean Coykendall, HUB International
Encouraging a culture of safety is something every member of the construction industry should make a priority.
That seems to be common practice here in Wisconsin, whose construction sector ranks in the top 10 of states for safety, according to U.S. Bureau of Labor Statistics data. That sets the state and its construction firms apart in one of the most dangerous businesses in the U.S., where a quarter of all work-related fatalities occur.
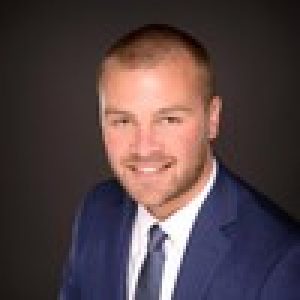
It takes a consistent focus to maintain that culture and safety record, though, which is bolstered by a well-thought-out and documented safety program. Here’s how to look at it.
An organization’s leadership – not just owners, but managers and supervisors – must set the tone, exemplifying the behaviors and commitment to health and safety that characterize the safety culture.
What should motivate everyone, of course, are the hazards that can seriously harm workers, whether slips, trips and falls, respiratory risks or “struck-by” hazards. But there should also be a shared concern over the damage incidents can do to the organization’s health and everyone’s livelihood. Serious accidents may result in a work stoppage that threatens the viability of the project and company.
"Construction firms will be well served by assessing the risks at each stage of each project and specifying the training and engineering controls to counter them."
Construction firms will be well served by assessing the risks at each stage of each project and specifying the training and engineering controls to counter them. Such due diligence is integral to an effective safety program. Here are three aspects to keep in mind.
- Safety program basics. A construction safety program should revolve around the goal of keeping workers safe and ensure they are able to respond quickly to hazards on the job – anticipated or not.
A well-documented program should be updated routinely and built around best safety practices in construction. This encompasses engineering controls – think cleaning protocols to avoid worksite clutter and safeguards like fencing around hazardous areas. Requirements for sufficient personal protective equipment should also be set out, whether helmets, goggles, gloves or ear plugs, as well as high-visibility vests. Safe-minded behaviors should also be reinforced. Standards set out by the Occupational Health and Safety Administration (OSHA) are a good basis for the program, but state and local regulations should also be included.
The program should reflect an investment in consistent safety training. That starts with project supervisor and managers, given their influence in establishing a safety culture. It should also emphasize the need for their heightened awareness of workers’ safety concerns and the value of recognizing and rewarding safe behaviors. Workers, too, must be trained, and that’s especially so with new hires who are likely lacking in the skills and experience and may need much closer supervision.
- Track the payoff. For every $1 invested in safety program, OSHA data has found as much as $6 can be saved through reduced illnesses, injuries and fatalities. Construction firms can benefit by tracking metrics to prove the point.
What to consider? Start with lagging metrics to use as benchmarks, like the Total Recordable Injury Frequency (TRIF) rate, or number of cases (per 100 full-time employees) where injury or illness cause an employee to be unable to work or to work with restrictions. Also helpful are leading indicators, such as the number of workers trained and reported near-misses. These support compliance and are helpful for signaling adjustments in the program.
The safety program’s incident reporting process is also important. It should be anonymous and allow for constructive feedback. Supervisors should be required to submit reports to help sharpen safety strategies.
- Prepare for OSHA inspections. The safety program should include guidance for inspections by regulators. These follow a typical pattern – a walk-around book-ended by opening and closing conferences. But the safety program should prepare supervisors for particulars. OSHA will, for example, require proof of hazard assessments and employee training. That’s why documentation of safety measures is crucial.
The OSHA compliance officer should be accompanied on inspections by an employee safety representative to explain protocols and address questions. It’s worth noting that they may question employees as well, so it’s important to prepare everyone for an inspection.
Sean Coykendall is Vice President of Commercial Insurance and Employee Benefits Consulting for global Top 5 insurance brokerage Hub International in Wisconsin.